Cómo apagar bombas de circulación de alta y baja temperatura sin causar daños: ilustrado con ejemplos
How to Shut Down High - Low Temperature Circulation Pumps Without Causing Damage: Illustrated with Examples
High - low temperature circulation pumps are essential pieces of equipment in many industries, such as chemical manufacturing, pharmaceutical production, and scientific research. They are designed to circulate heat - transfer fluids at both high and low temperatures to maintain precise temperature control in various processes. However, improper shutdown of these pumps can lead to significant damage, including mechanical wear, damage to seals, and even failure of the pump motor. Here are some guidelines and real - world examples on how to shut down high - low temperature circulation pumps correctly.
1. Gradual Temperature Reduction
Case Example
In a chemical plant, a high - low temperature circulation pump was used to circulate a heat - transfer fluid for a reaction process that operated at high temperatures. One day, due to an emergency, the operator quickly shut down the pump without reducing the temperature first. As a result, the sudden drop in temperature caused the metal components of the pump to contract rapidly. This led to misalignment of the impeller and the pump casing, and the seals were also damaged due to the uneven stress. The next time the pump was started, it made a loud noise and leaked fluid, indicating serious damage.
Correct Procedure
To avoid such issues, before shutting down the pump, the temperature of the system should be gradually reduced to a safe level. This allows the metal components of the pump to cool down evenly and slowly. For example, in a typical chemical process, if the operating temperature is 150°C, the temperature can be decreased in steps, such as reducing it by 10 - 15°C every 10 - 15 minutes. This gives the pump enough time to adjust to the temperature change, minimizing the risk of thermal stress - induced damage.
2. Proper Fluid Handling
Case Example
A research laboratory was using a high - low temperature circulation pump for a cryogenic experiment. When the experiment was completed, the operator simply shut off the pump without taking any measures regarding the cryogenic fluid. Over time, the fluid in the pump solidified, clogging the impeller and the pipelines. When the pump was started again for the next experiment, the motor was unable to turn the impeller due to the blockage, and the motor windings overheated and burned out.
Correct Procedure
Before shutting down the pump, it is crucial to handle the heat - transfer fluid properly. If the fluid is a cryogenic liquid, it should be drained from the pump and the system in a controlled manner. This may involve using a special drainage system or following specific procedures to ensure that the fluid is safely removed. For high - temperature fluids, make sure that the fluid is allowed to cool down to a point where it will not cause damage during the shutdown process. Additionally, in some cases, it may be necessary to flush the pump with a suitable cleaning fluid to prevent any residue from solidifying or causing blockages.
3. Sequential Shutdown
Case Example
In a pharmaceutical manufacturing facility, a high - low temperature circulation pump was part of a complex temperature - control system. One day, an operator shut down the pump without following the proper sequence. The pump was connected to a series of valves and other components in the system. By shutting down the pump first without closing the relevant valves, the pressure in the system became unbalanced. This caused backflow of the fluid, which damaged the non - return valves and also put excessive stress on the pump's seals.
Correct Procedure
A sequential shutdown procedure should be followed. First, close the inlet and outlet valves of the pump gradually to control the flow of the fluid and maintain the pressure balance in the system. This prevents backflow and the associated damage. After the valves are closed, then turn off the power to the pump motor. In a more complex system with multiple components, it may be necessary to follow a detailed shutdown flowchart provided by the equipment manufacturer. This ensures that each component in the system is shut down in an order that minimizes the risk of damage.
4. Post - Shutdown Inspection
Case Example
In an industrial heating system using a high - low temperature circulation pump, the operator shut down the pump according to the standard procedure. However, no post - shutdown inspection was carried out. After a few days, when the pump was restarted, it was found that a small leak had developed in one of the pipe joints. This was due to a minor crack that occurred during the shutdown process, which could have been detected and repaired if a post - shutdown inspection had been performed.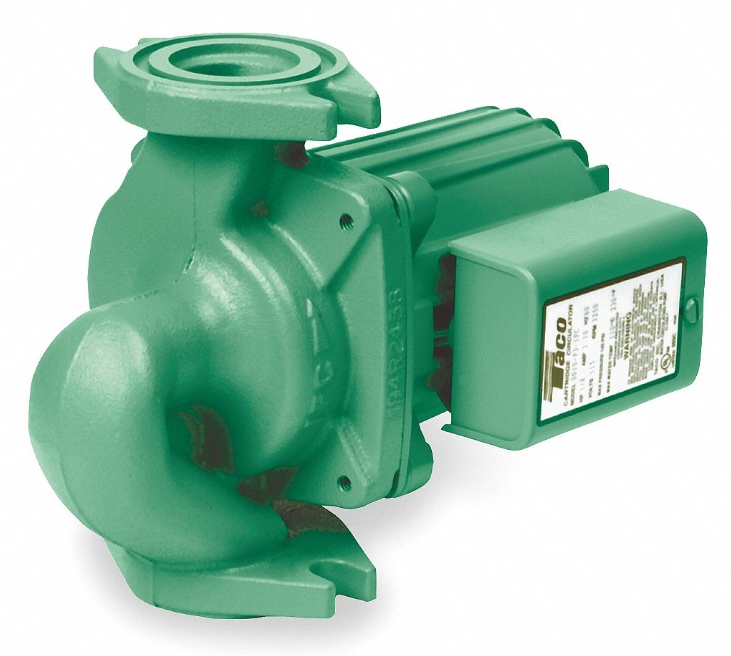
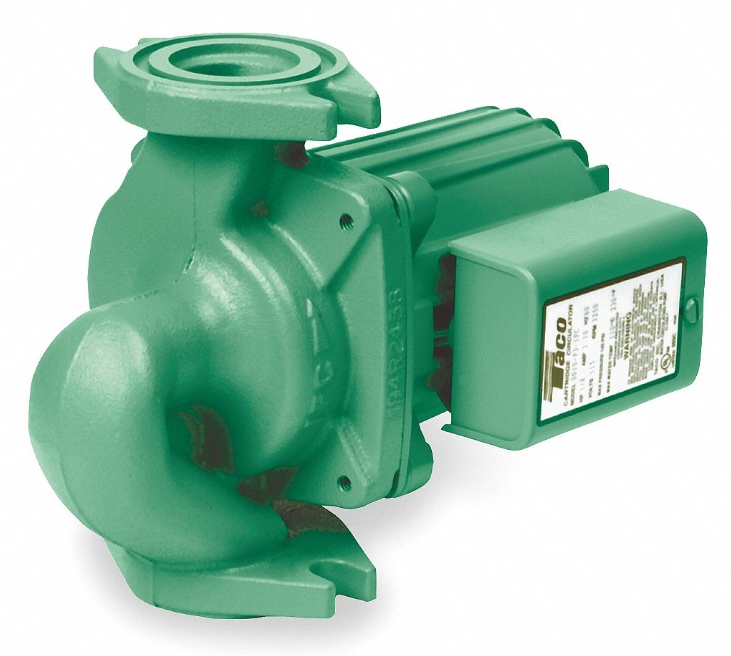
Correct Procedure
After shutting down the pump, a thorough inspection should be carried out. Check for any signs of leakage in the pump, pipes, and connections. Inspect the impeller for any signs of damage or wear. Also, check the electrical components, such as the motor and the control panel, for any abnormal conditions. If any issues are detected during the inspection, they should be addressed immediately to prevent further damage when the pump is restarted.
In conclusion, proper shutdown of high - low temperature circulation pumps is just as important as their proper operation. By following the correct procedures, such as gradual temperature reduction, proper fluid handling, sequential shutdown, and post - shutdown inspection, users can avoid costly damage to the pumps and ensure their long - term reliability. Each industry and application may have specific requirements, but these general principles can be applied across the board to safeguard the integrity of high - low temperature circulation pumps.